Nearly four decades ago, Dwight Miller climbed an electric utility pole to rescue a fellow lineman who had accidentally made contact with an energized line. The injuries were bad, and although the lineman survived, the scene haunted Miller’s sleep for weeks.
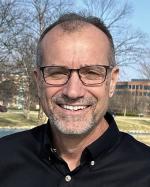
“It totally changed my outlook on everything. I became an advocate for safety that day,” says Miller, who was working for a private contractor at the time, but today is the senior director of safety training and loss prevention for Ohio’s Electric Cooperatives, the statewide trade association that provides services for the 25 electric distribution cooperatives in Ohio and West Virginia.
On an electric lineworker crew, it’s everyone’s job, he says, to make sure everyone is following the lifesaving basics: wearing protective rubber gloves and sleeves, testing and grounding lines, using proper line cover-up practices, and line clearance.
Miller’s laser focus on safety — whether in an official capacity or “just speaking up when nobody else would speak up” — altered his career path.
Culture of safety
Today, Miller’s nine-member safety team works in Ohio and West Virginia to coach, train, and support not only the 375 lineworkers employed by the co-ops, but all 1,500 cooperative employees in the state, with an aim to keep everyone safe.
He says the support his team receives from engaged cooperative leaders has led to a significant decrease in injuries over the years. In fact, the number of workdays missed or work restricted at the co-ops due to injury (a common industry metric) has been more than halved since 2004.
For Miller, though, it’s still not enough, and he consistently cautions company leaders to be ever vigilant.
“We’re happy to see good numbers, but we urge everyone to focus on the idea that hazards are there every day, just waiting for someone, somewhere,” he says. “They must be prepared when and if problems arise.”
One aspect of the safety team’s job is to implement RESAP — the Rural Electric Safety Achievement Program — a national initiative led by the National Rural Electric Cooperative Association. RESAP involves a periodic intensive review of cooperative safety practices with a goal of continual improvement. Combined with Commitment to Zero Contacts, a complementary program focused on lineworkers, RESAP helps cooperatives build — and maintain — their safety culture.
It’s everyone’s job
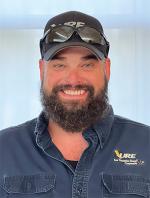
Sean Luellen says lineworker training has become more focused on safety since he began his career a quarter-century ago. A crew leader for the lineworkers at URE–Union Rural Electric Cooperative in Marysville, Luellen says the “old school” attitude from some supervisors used to be “Do as I say, not as I do.”
Today, training for both apprentice and journeyman lineworkers, whether it takes place within individual cooperatives or at the Central Ohio Lineworker Training facility in Mount Gilead, puts safety ahead of everything else, and Luellen says that commitment is exemplified by NRECA’s “Speak Up, Listen Up” program.
“It’s one of our pillars of safety,” he says. “Everyone on the job has stop-work authority. That’s exactly what our culture of safety is here. We try to instill in our crews, ‘You have a voice.’”
It’s everyone’s job, he says, to make sure everyone is following the lifesaving basics: wearing protective rubber gloves and sleeves, testing and grounding lines, using proper line cover-up practices, and line clearance. “These are the things we do so if something unexpected were to happen, it’s not going to be something that stops a guy from going home at night.”
Safety at the source
The safety culture at co-ops is shared by the men and women who work at the Cardinal Power Plant in Brilliant, the 1,800-megawatt generating station that produces most of the affordable, reliable power that keeps members’ lights on.
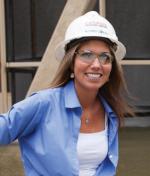
“We always ask, ‘Is it compliance or are you committed?’” says Bethany Schunn, plant manager. “A lot of things we do, we do because of compliance, but when it comes to safety, we want to make it a commitment.”
In addition to the high-voltage electricity flowing out of the plant, the 250 Cardinal employees face risks common to any large industrial workplace — heat, cold, caustic chemicals, open holes, moving heavy equipment, and more.
Because research has shown that workers identify only 45 percent of possible hazards on the job, the Cardinal Plant in 2023 adopted the Energy Wheel, a practice of regularly reviewing a range of potential safety threats such as biological, chemical, and mechanical hazards.
“It’s a structure we apply to our already existing safety culture,” Schunn says. “It’s a way of jogging everyone’s memory. And it’s not just about identifying hazards, but we also talk about what we’re going to do to minimize the hazards and keep someone from getting hurt.”
Making year-against-year comparisons is difficult, Schunn says. But in 2020, workers at the facility suffered four injuries that resulted in a total of 369 workdays missed or restricted. In 2024, only one such injury occurred, resulting in a total of 38 days away from work.
“Since we just started utilizing the Energy Wheel, I can’t attribute our decline since 2020 solely to that effort,” she says. “However, we hope to keep focusing on our safety culture and keep getting better, and safer.”